The Cost Savings of Outsourcing Your Fulfillment to a 3PL
- John Lermi
- Sep 9, 2024
- 4 min read
For e-commerce businesses, logistics and fulfillment are critical aspects of the operation that can significantly impact profitability. Managing fulfillment in-house can seem like a way to control costs, but as your business grows, the complexity and expense can quickly spiral. This is where a Third-Party Logistics (3PL) provider becomes invaluable. By outsourcing fulfillment to a 3PL, businesses can reduce operational costs, improve efficiency, and free up resources to focus on growth.
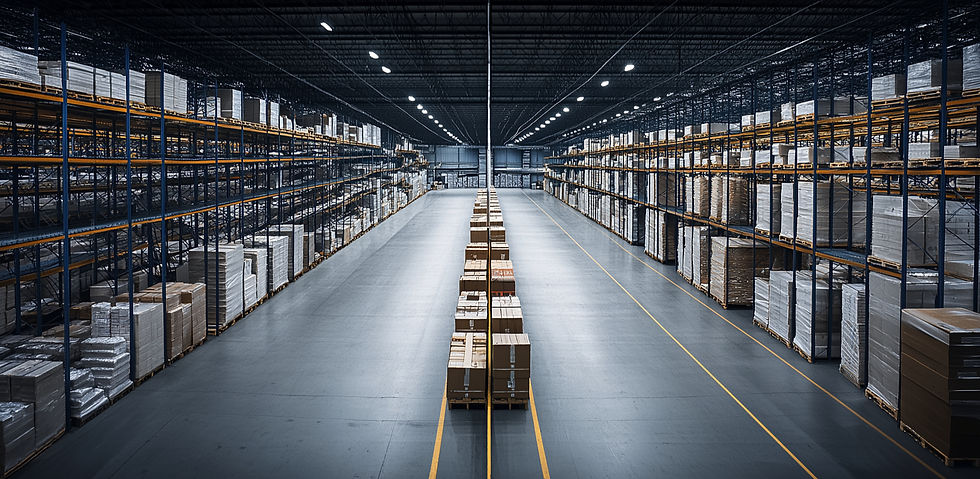
Infrastructure and Warehousing Costs
One of the most significant expenses associated with in-house fulfillment is the cost of physical infrastructure. Maintaining a warehouse or storage facility requires capital investment, ongoing rent or mortgage payments, and utility costs.
In-House Fulfillment Costs:
Warehousing Space: Renting or buying warehouse space is a considerable expense, especially in high-demand locations. On top of that, additional costs include heating, electricity, and security.
Maintenance and Upkeep: Regular maintenance is required for the upkeep of equipment, storage systems, and facility improvements.
Inventory Storage: Seasonal inventory surges can require additional space, which may lead to excess costs during slower seasons when that space is not fully utilized.
3PL Fulfillment Costs:
Scalable Warehousing: With a 3PL provider like PINAKL FBA, businesses pay for only the space and services they use, allowing for flexibility during peak seasons and avoiding the need to maintain unused space.
No Capital Investment: There’s no need to invest in long-term property or expensive warehouse technology. These expenses are borne by the 3PL, allowing businesses to avoid upfront costs.
Labor and Workforce Management
Managing in-house fulfillment requires a dedicated workforce to handle picking, packing, shipping, and customer service. Labor costs can quickly accumulate, particularly as order volume increases.
In-House Fulfillment Costs:
• Hiring and Training: Recruiting, training, and managing a fulfillment team is not only time-consuming but also costly. As volume increases, more employees must be hired to keep up with demand.
• Payroll and Benefits: Full-time staff members come with ongoing payroll costs, health benefits, insurance, and taxes.
• Overtime and Seasonal Hiring: During peak seasons, businesses often have to hire temporary staff or pay existing employees overtime, which further increases labor costs.
3PL Fulfillment Costs:
• Variable Labor Costs: With a 3PL, businesses only pay for the labor required to fulfill their orders. As volume increases or decreases, labor costs adjust accordingly without the need to manage hiring or overtime.
• No Overhead for Employee Benefits: 3PL providers handle their own workforce and assume the costs of labor management, freeing businesses from these expenses.

Shipping and Transportation Costs
Shipping is another significant cost for businesses, particularly for those with a high volume of orders. In-house shipping often lacks the leverage needed to negotiate favorable rates with carriers.
In-House Fulfillment Costs:
• Higher Shipping Rates: Without the scale of larger operations, businesses may face higher shipping rates and slower delivery times due to lower negotiating power with carriers.
• Lack of Strategic Locations: Businesses with limited fulfillment centers may struggle to offer fast and affordable shipping across wide geographic regions, increasing costs for both the business and its customers.
3PL Fulfillment Costs:
• Discounted Shipping Rates: 3PL providers have established relationships with major shipping carriers and leverage large shipping volumes to negotiate discounted rates, allowing businesses to save on transportation costs.
• Faster Shipping Options: With multiple strategically located fulfillment centers, 3PLs can offer faster and more affordable shipping across various regions, enhancing customer satisfaction while reducing costs.

Technology and Equipment Costs
Running an efficient fulfillment operation requires the right technology to track inventory, manage orders, and coordinate shipping. Investing in this technology in-house can be expensive and require ongoing updates and maintenance.
In-House Fulfillment Costs:
• Software Systems: Inventory management, order tracking, and shipping software can be expensive to implement and maintain.
• Automation and Equipment: Purchasing and maintaining fulfillment equipment like conveyors, barcode scanners, and packaging machines adds additional costs, particularly if the business plans to scale.
3PL Fulfillment Costs:
• Access to Advanced Technology: 3PL providers invest in cutting-edge logistics technology and provide it as part of their service package. This means businesses can benefit from real-time inventory management and order tracking without the need to make heavy investments in software or equipment.
• No Equipment Investment: All necessary fulfillment equipment is provided by the 3PL, so businesses avoid the upfront costs and ongoing maintenance fees.
Reduced Risk and Errors
Managing fulfillment in-house comes with its fair share of risks, including shipping delays, inventory mismanagement, and costly returns. These errors can damage a business’s reputation and lead to increased costs for replacements or refunds.
In-House Fulfillment Costs:
• Human Error: Mistakes in packing, shipping, or inventory management can result in financial losses and reputational damage.
• Return Costs: Handling returns internally requires additional staffing and systems to manage the reverse logistics process efficiently.
3PL Fulfillment Costs:
• Efficient Order Accuracy: 3PL providers like PINAKL FBA are experts in logistics and use best practices to minimize errors in order fulfillment.
• Streamlined Returns: Outsourcing returns management to a 3PL reduces the burden on in-house staff, saving time and resources while ensuring a positive customer experience.
Conclusion
When comparing the costs of in-house fulfillment versus outsourcing to a 3PL provider, the financial benefits of outsourcing are clear. By leveraging the expertise, infrastructure, and technology of a 3PL provider like PINAKL FBA, businesses can reduce overhead costs, improve efficiency, and gain the flexibility needed to scale their operations.
For e-commerce businesses looking to streamline their fulfillment operations and focus on growth, outsourcing to a 3PL is not just a smart move—it’s a financially sound one. If you’re ready to explore how PINAKL FBA can help your business save on fulfillment costs, contact us today for a free quote.
Comments